Supply Chain Disruption: Three Questions with Dr. Alvin Williams
Posted on November 19, 2021
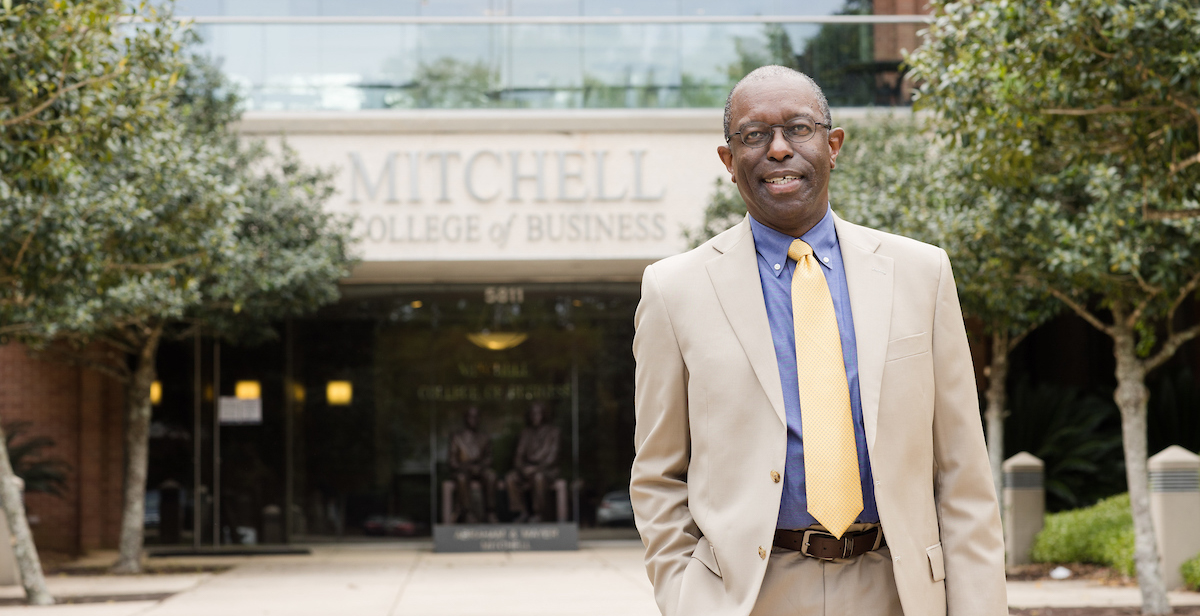
At the University of South Alabama, questions about the global supply chain go to Dr. Alvin Williams, interim dean of the Mitchell College of Business and a former editor of the Journal of Supply Chain Management.
His academic research includes everything from purchasing strategies and management training to the role of truck drivers as an under-appreciated link in the supply chain.
Williams, a distinguished professor of marketing, is a past president of the Society for Marketing Advances. He has presented papers and led seminars at more than 300 conferences in the United States, Europe and Asia.
At the Mitchell College of Business, which offers a major in Supply Chain and Logistics Management, Williams found time for a question-and-answer session on supply chain issues as the country heads into the busy holiday season.
What’s the big picture on the supply chain problems we hear so much about in the news?
“A starting point is that we all have to recognize the interconnectedness of the global economy. People in Mobile are dependent on companies in Shanghai. People in Tokyo are dependent on companies in Chicago. I’m not sure we should call it a supply chain so much as a supply network, because that embodies more of the complexity we’re talking about. If you look at the interruption that we had during the COVID year, many supply chains were functioning at half capacity, or 25 percent capacity, and now they’re trying to ramp up, and you’ve got these choke points and bottlenecks. If you look particularly at the ports of Los Angeles and Long Beach, you have more supplies coming in than people to handle them.
“The idea that you’ve got consumer goods in ships off the coast of California, but not on the store shelves of Mobile, that’s a big problem. Something as simple as Christmas toys, most stores put in their orders by July. You can’t just run to the factory and crank out another 300,000 puzzles, or dolls, or tricycles. Those orders have been placed and they’re somewhere in the supply chain, hopefully running on time, but maybe not.”
So there are shortages and delays going into the busiest shopping time of the year. Are there any alternatives to the global supply chain?
“It’s interesting, some of the conversations about where we’re going from here. You know, do we try to bring production back to the U.S.? That sounds good, but it’s not going to happen in a very big way because it’s far too costly. Take any basic T-shirt you can get for 10 or 12 bucks, and it’s made somewhere else. If it was made in America, it might be a $35 T-shirt. The question becomes, are you willing to pay that? And everyone’s going to say ‘No.’
“In the short run, we all have the same anxieties, the same uncertainties. In the long run, these supply chains will bounce back and allow for the smooth flow of goods and services that we’ve known in the past. Long-term could be a couple of years in some cases. I don’t think there will be one model for every single product.”
Is this the year of shipping delays, and then we all move on, or will we still be talking about the supply chain next Christmas?
“Oh, yes. This conversation isn’t going away. This conversation will become more pointed and more focused, but it’s not going away.”